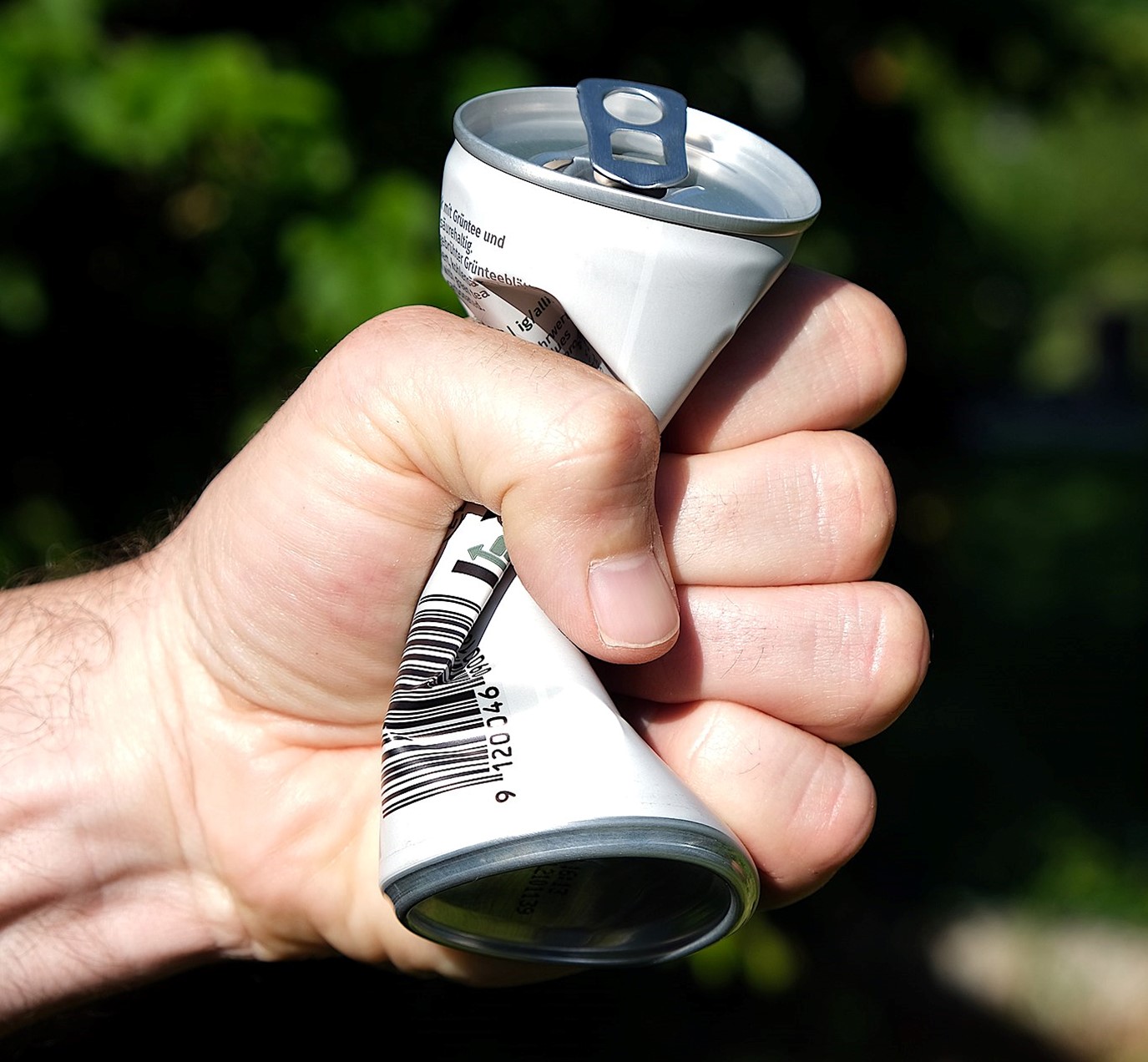
Credit: Miriam Rundel, CC BY-SA 4.0, via Wikimedia Commons
If you were to design the perfect industrial material, what would it be like?
You’d want it to be strong and lightweight. Easy to form into different shapes. You’d like it to be resistant to corrosion. And to heat.
Ideally, you could easily combine it with other materials for more uses. And re-uses.
It would be best if all these qualities came in something cheap and abundant.
And in fact, they do. This ideal material … is aluminum.
It’s the third-most abundant element in Earth’s crust, behind oxygen and silicon. It’s a small, highly charged atom, so it bonds well to others to form valuable alloys.
Adding even a small fraction of copper makes aluminum much harder, for use in things like jet engines.
A little magnesium makes it much more malleable, for things like packaging.
A little boron raises aluminum’s electrical conductivity almost to that of copper, to make a cheaper, lighter wire ideal for transmission lines.
It’s made from bauxite ore, in a process that requires a great deal of electricity. But it takes only 5% of that energy to recycle it.
As a result, of the nearly 1 billion tons of aluminum ever produced, three-quarters of it is still in use—recycled in a closed loop so that its many benefits can be enjoyed again and again. That truly is an ideal material.
Background
Synopsis: Lightweight, corrosion-resistant aluminum is one of the world’s most plentiful and useful metals. It is conductive, nonmagnetic, soft, malleable and strong, especially when alloyed with other metals. We use it every day in drink cans, cooking foil, household wiring, jet engines, ships, skyscrapers and more. Producing it from ore requires a lot of processing, but it is easily recycled—more than 75% of all the aluminum produced since 1880 is still in use.
- Aluminum (Al) is a silver-gray metal that is lightweight, durable, corrosion-resistant, rustproof, nontoxic, nonmagnetic, easy to work into new shapes and able to conduct electricity while reflecting light and heat effectively.
- Is it aluminum or aluminium? Both. In 1925, the American Chemical Society adopted the name of the element as “aluminum” in the United States, then in 1990, the International Union of Pure and Applied Chemistry (IUPAC) officially designated "aluminium" as its spelling, which is now used outside of the United States.
- The chemical element aluminum has an atomic number of 13 and an atomic mass of 26.98. Its melting point is 1,220°F (660°C).
- When aluminum is combined with other metals into alloys, it becomes very strong, making it the second-most popular metal for building things after iron and its alloy, steel.
- Its low density of 2.7 g/cm3 is only about one-third that of steel or copper, while pure aluminum is about 60% as conductive as copper, and its alloys get even closer to equivalent conductivity.
- The aluminum atom is small and highly charged, so it forms strong bonds, especially with oxygen.
- When exposed to air, it quickly forms a ghostly white protective layer of aluminum oxide (Al2O3). Without any iron (Fe), it cannot oxidize into rust (FeO2).
- Aluminum oxide is the mineral known as corundum, which forms rubies and sapphires with impurities of chromium and iron, respectively.
- Because of its reactivity, aluminum is rarely found in its elemental state but is common in oxides and silicates. This causes it to be bound into rocks in Earth’s crust in minerals like feldspars and aluminosilicates that are the most common minerals in Earth’s crust.
- At 8.2%, aluminum is the third-most abundant element in Earth’s crust after oxygen (46.1%) and silicon (28.2%). It is 46% more common in the crust than iron and 1,200 times as common as copper.
- Aluminum tends to stay in Earth’s crust because of its affinity for oxygen, while less-reactive metals sink into the mantle, where aluminum is the sixth-most abundant element at 2.29%, after oxygen, magnesium, silicon, iron and calcium.
- Earth’s core is made up almost entirely of iron and nickel.
- Overall, aluminum makes up about 1.59% of Earth’s total mass, the eighth-most abundant element after iron, oxygen, silicon, magnesium, sulfur, nickel and calcium.
- Since it doesn’t occur as the pure metal naturally, aluminum must be refined from an aluminum ore called bauxite. A less energy intensive alternative is to recycle it from previously processed aluminum.
- Bauxite is not a mineral; it is a hydrated alumina rock that forms from the weathering of minerals like feldspar in tropical climates where silica is leached away to form laterites.
Bauxite from Les Baux-de-Provence, France, and a piece of aluminum metal, with U.S. pennies for comparison. Bauxite forms as a rind on the rock fragments in this conglomerate.
Left Credit: U.S. House Committee on Natural Resources, public domain, via Wikimedia Commons
Right Credit: USGS Mineral Resources Program, public domain - The world has between 55 billion and 75 billion tons of bauxite resources for the future.
- It takes about four times the weight of bauxite to produce a given weight of aluminum.
- Globally, nearly 400 million tons of bauxite are mined every year, and 85% of that is used to make aluminum metal. Australia, China and Guinea produce 72% of the world’s bauxite.
- After extraction, about 85% of the ore is sent to refineries for the next step.
- Bauxite is not a mineral; it is a hydrated alumina rock that forms from the weathering of minerals like feldspar in tropical climates where silica is leached away to form laterites.
- Aluminum is difficult to extract from rock, so it has only been produced commercially for about 130 years. It requires two processes: the first to turn ore into alumina, and the second to turn alumina into aluminum metal.
- In the first step, the ore is crushed and heated with sodium hydroxide under pressure to dissolve out the aluminum oxide, which is filtered and precipitated as aluminum hydroxide (Al(OH)3). Then, the aluminum hydroxide is heated to form sandy white crystals of Al2O3 called alumina. This is the Bayer process, which was invented in 1888. China, Australia, Brazil and India supply most of the world’s alumina.
Because of its hardness of 9 on the Mohs scale (diamond is 10), some alumina (corundum) is used as an abrasive for products like sandpaper or as proppants for oil and gas extraction.
Credit: Dorgan (assumed), CC BY-SA 3.0, via Wikimedia Commons - In the second step, smelters split alumina molecules into oxygen atoms and aluminum metal by passing strong electrical currents through a bath of molten cryolite (Na3AlF6), requiring a lot of electricity. Pure aluminum settles into the bottom of the cell as a liquid. This process was developed in 1886 and is called the Hall-Héroult process. China, India, Australia and Russia lead the world in aluminum production.
- Commercial ingots of aluminum are huge and can weigh as much as 30 tons.
- In the first step, the ore is crushed and heated with sodium hydroxide under pressure to dissolve out the aluminum oxide, which is filtered and precipitated as aluminum hydroxide (Al(OH)3). Then, the aluminum hydroxide is heated to form sandy white crystals of Al2O3 called alumina. This is the Bayer process, which was invented in 1888. China, Australia, Brazil and India supply most of the world’s alumina.
- When aluminum is mixed with just 1% to 10% of other metals, the resulting aluminum alloys have enhanced properties.
- For lightweight, strong, hard-wearing, high-temperature applications, like automobile or jet engines, aluminum is combined with copper.
- For strong, malleable uses, like aluminum foils for food packaging, aluminum is alloyed with magnesium.
- For lightweight electrical transmission when copper is too heavy or expensive, mixing boron into aluminum produces power cables with almost the same electrical conductivity as copper, and the lighter lines don’t droop as much on hot days.
- Hard, yet light, aluminum alloys first appeared in the early 1900s and became critical strategic resources during both World Wars for strong, light airframes and other military applications.
The B-17 Flying Fortress bomber first took to the skies in 1935. Here, the Aluminum Overcast arrives at MacDill Air Force Base, Florida, in 2003. The B-17's reputation for indestructibility is the result of testing, innovative engineering and aluminum airframe materials.
Credit: National Archives at College Park—Still Pictures, public domain, via Wikimedia Commons - Sputnik 1, the first spacecraft to orbit Earth in October of 1957, was made of two hemispheres of an aluminum-magnesium-titanium alloy. All spacecraft since then have used aluminum alloys to some extent.
Replica of Sputnik 1 in the Museum of Space Exploration and Rocket Technology in Saint Petersburg, Russia. It was a polished metal sphere 23 inches (58 centimeters) in diameter that was launched into an elliptical low-Earth orbit by the Soviet Union on October 4, 1957, as part of the Soviet space program. It sent a radio signal back to Earth for three weeks before its three silver-zinc batteries ran out. Aerodynamic drag caused it to fall back into the atmosphere on January 4, 1958. The hemispheres were 2 millimeters thick and were covered with a highly polished 1-millimeter-thick heat shield made of an aluminum-magnesium-titanium alloy, AMG6T.
Credit: Andrew Butko, CC BY-SA 3.0, via Wikimedia Commons - Aluminum alloys became a civil engineering workhorse material for both structural and cosmetic building applications in the middle of the 20th century.
- While a few cars, like the Audi A-8, have used aluminum frames in the past, in 2015 Ford produced its popular F-150 pickup truck with an all-aluminum body, reducing its weight by 40% and dramatically improving fuel consumption.
- Today, aluminum has many uses and is important in virtually every segment of the economy. The demand for aluminum is expected to double over the next 10 years.
- Every year, about 40% of American aluminum consumption feeds the transportation industry, going into parts for vehicles including automobiles and airplanes, trucks and railcars, and even marine vessels.
- About 21% is used to produce packaging in the form of cans and foil products.
First produced in 1913, a roll of everyday kitchen aluminum foil. Aluminum foil is typically less than 6 one-thousandths of an inch (0.15 millimeters) thick. It can be about 15 times thinner—as thin as 4 ten-thousandths of an inch (0.01 millimeter)!
Credit: MdeVicente, CC0, via Wikimedia Commons - Around 14% of American aluminum consumption goes to construction, including windows, doors, roofs and siding.
- Electrical transmission lines consume about 8% of the aluminum used in the United States today.
- Consumer durables like pots and pans, utensils and appliances take 7%, and machinery and tools take another 7%.
- The global aluminum market in 2021 was $246 billion, and it is expected to double by 2030 to $498 billion as lightweight materials increase in importance.
- One of the most familiar aluminum products is the aluminum beverage can. Today, the average U.S. household uses 208 aluminum cans per year.
- The aluminum can was invented in 1956 and was used for portable drink storage starting in 1958. The shelf life and durability of these containers is outstanding.
- Aluminum is great for cans because its malleability makes them easy to manufacture by rolling and stamping.
- This same characteristic makes them easy to crush and recycle, so cans are currently the most recycled beverage container.
- With costly and energy-intensive mining, refining, and processing, recycling of aluminum is attractive because it takes about 20 times less energy to produce and is a much quicker process.
- Aluminum recycling began in the early 1900s and was popular during wartime, but really took off in the 1960s with the introduction of easy-to-recycle beverage cans.
Aluminum recycling efforts were important during World War II to produce new military equipment and consumer goods. This 1941 photo is from the New York City Aluminum Collection.
Credit: National Archives and Records Administration, public domain, via Wikimedia Commons - Since 1880, 900 million tons of aluminum have been produced, and more than 75% of that metal is still in use.
- While glass and plastics are usually “down-cycled” into products like landfill liner or carpet fibers, aluminum cans are truly “re-cycled” over and over again in a closed loop. This makes them more valuable to recyclers.
U.S. production of aluminum from ore, new scrap, and old scrap, 1940-2014. Data from the U.S. Geological Survey.
Credit: Plazak, CC BY-SA 4.0, via Wikimedia Commons - Aluminum cans contain 73% recycled content on average, compared to 23% for glass and 6% for plastic.
- In addition to beverage cans, recycled aluminum can be sourced from household waste, cars and building materials.
Cuboids of crushed cans recycled at Oregon State University in 2009.
Credit: Oregon State University, CC BY-SA 2.0, via Wikimedia Commons